Lurking Environmental Dangers of Manufactured Gas Plants
Manufactured gas plants (MGPs) were pivotal fixtures in local power generations from the early 1800s to the mid-1900s.1 As the name suggests, MGPs produced gas which could be stored, distributed and used for heating, cooking and lighting, similar to natural gas use today.
Although historically terminated, MGPs environmental impacts remain today. Regardless of the duration or when the operation ceased, the impacts of MGPs continue to generate long-term harm to the environment and have the potential to incur liability cost to property owners.
History of Manufactured Gas Plants
The first successful attempts to create a manufactured gas occurred in France and England around 1800. The first MGP utility was founded in England in the 1820s, and soon followed by other MGPs across Europe and the United States.2
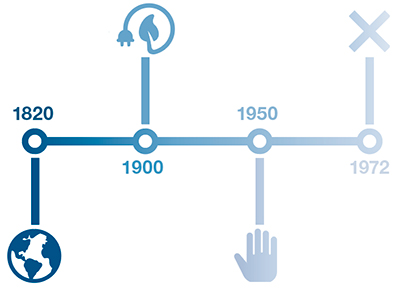
MGPs typically existed in towns with populations greater than 5,000 residents and were commonly referred to as “town gas.”3 More densely populated cities commonly had multiple MGPs. In the early 1900s, many MGP locations began closing in favor of cheaper energy alternatives as oil resources and refining developed, and electric power networks grew nationwide. By the 1950s, most (but not all) MGP operations had ceased. In New York, for example, the last MGP was not shuttered until 1972.4
MGP Process
The gas manufacturing process varied based on the size and age of the MGP operation, but it generally involved heating a hydrocarbon-based feedstock, typically coal, in a sealed oven-like structure, where the anaerobic conditions prevented the feedstock from burning. This process, known as carbonization, produces volatile gasses, which can be collected, purified and stored for later use as fuel for heating, cooking and lighting. Oil and other feedstocks may also be used in place of coal.5
The gasses generated contained moisture and particulates. MGP gasses were typically sent through condensers where the moisture and particulates could settle out as a by-product. The moisture and coal particulates formed a black viscous substance more commonly referred to as coal tar.6 Prior to entering the gas holding tank, other gaseous impurities like ammonia were removed by ‘washing’ the coal gas in water. It was common to have additional coal tar settle out during the washing and holding process.7
MGP Residual Contaminants
Former MGP operations have left residual contamination in two main forms:
- Coal Tar
- Purifier Waste
Coal Tar
As described above, coal tars were a primary waste by-product of an MGP’s manufacturing process. The term coal tar is a broad classification of oily, non-aqueous phase liquid (NAPL) MGP residuals, which tended to be more of a flowable liquid than a true sticky, viscous “tar,” although some MGP processes did create more viscous tar-like by-products.8 Regardless, the term coal tar is widely used when referring to MGP contaminants and will be retained for congruity.
When released to the ground surface or subsurface, coal tar migration is primarily affected by gravity and will migrate downward through soils.
Purifier Waste
Unlike coal tars, purifier waste does not migrate once placed in the subsurface. Purifier waste turns green or blue in color and will have solid tar material bound to the fibrous media.9 Purifier waste impacts come as a result of leaching. Complex cyanide compounds will leach from the purifier waste and impact groundwater.10 MGP cyanide contamination will move through the subsurface with the natural groundwater flow. Leaching from purifier waste can also cause groundwater to become highly acidic. Depending on the characteristics of the surrounding area, highly acidic groundwater can erode subsurface structures and/or cause biologic harm for nearby surface waters.11
Characterizing MGP Residuals
Most MGP residuals have easily identifiable physical characteristics, such as color, odor and viscosity, and often they can account for a significant percentage of the overall subsurface matrix. Coal tar oils and feedstock oils for the oil-gas MGP process are typically much more viscous than most fuel or lube oils, and the odor of coal tar oil is very distinct from petroleum oil. Additional characteristics include:12,13
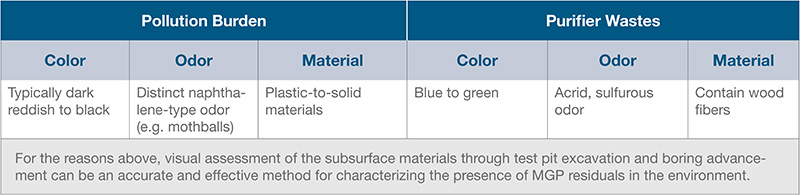
Visual and olfactory assessment generates a large volume of information concerning the nature and extent of MGP residuals in a relatively short period of time and reduces the need for extensive laboratory analysis. Laboratory analysis helps to confirm field observations, provide quantitative values for risk assessment, confirm the limits of MGP residuals, and distinguish MGP residuals from other anthropogenic materials in complex environmental matrices.
Learn more about the characterize following laboratory analyses are typically used to help characterize MGP residuals in soil, groundwater, surface water, and sediment:
Remediation of MGP Contaminants
MGP remediation is determined based on multiple site factors including subsurface geology, depths of impacts, NAPL mobility and proximity to potential receptors. Typical remediation includes a combination of excavation with engineering and institutional controls. Excavation and disposal of shallow soils impacted by former MGP operations and backfilling with a clean fill cap removes the potential for direct exposure.
Want to learn more about the importance of Clean Fill? More information on the examination of the impact of using contaminated fill can be found here.
Additional Considerations
Odor
Although MGP operations ceased decades ago, and residual contamination is buried in the subsurface, sometimes residual MGP odors can be detected in the air in the vicinity of the former MGP location, particularly on warmer days. MGP odors can be a nuisance and raise public awareness and concern of MGP sites, particularly during remediation activities. Excavations and other remediation activities at MGP sites often require odor mitigation/suppression measures and community outreach.
There are two broad categories of odors that may be present at a former MGP site:
Environmental Protection
While evaluating if potential contamination has been adequately characterized at a property that is located on or in the vicinity of a historic MGP site, it is important to work with a knowledgeable carrier who can consider any state-level programs which may be applicable and help properly mitigate the risks described above. Contact your underwriter today to learn more about how our core products and services can help protect your clients’ operations.
Resources
https://www.pge.com/en_US/about-pge/environment/taking-responsibility/manufactured-gas-plants/mgp.page
https://www.dec.ny.gov/chemical/24911.html
https://www.njresources.com/community/environment/manufactured-gas-plants/index.aspx
https://www.dec.ny.gov/chemical/24922.html